Regeneracja jednej z płytek PCB wchodzącej w skład modułu procesora sterownika CP60 firmy B&R.
Jakiś czas temu do naszego serwisu Klient dostarczył niedziałający, acz mocno już wiekowy sterownik CP60 firmy B&R.
Płytki PCB tego sterownika są przystosowane do montażu ołowiowego THT i posiadają dwie warstwy miedzi (top & bottom sides) spojone dobrej jakości laminatem. Okazało się też, że posiadają one nitowane przelotki ale są dosyć odporne na obciążenia termiczne podczas lutowania, co bardzo dobrze rokuje przy wykonywaniu regeneracji i napraw.
W trakcie diagnozy okazało się, że jedna z płytek drukowanych (PCB) wchodząca w skład modułu CPU uległa zalaniu cieczą, najprawdopodobniej wodą. W efekcie czego, przy udziale wysokich temperatur panujących podczas pracy, powstał potężny nalot tlenków, czyli jak mówimy wtedy „masywna korozja PCB”. Po ustaleniu i zaakceptowaniu kosztów przystąpiliśmy do naprawy, polegającej w tym przypadku na usunięciu utlenionych połączeń oraz wymianie elementów, w których utlenione były wyprowadzenia.
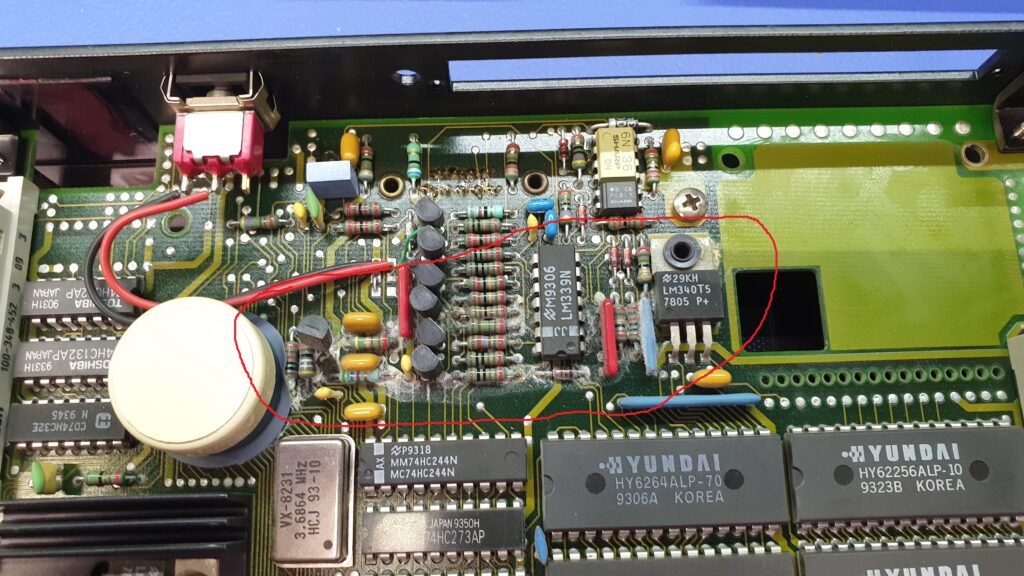
Na zdjęciu powyżej, czerwoną obwódką został zaznaczony obszar objęty regeneracją.
Widać tam wyraźnie szary nalot, który występuje na praktycznie wszystkich elementach tego obszaru, a co gorsza także i pod nimi. Widać to jeszcze lepiej na obrazach poniżej. Tam też można zaobserwować, że niektóre z elementów (np. układ scalony LM339N lub tranzystory po jego lewej stronie) nadają się do wymiany z powodu potężnie skorodowanych nóżek (pinów).
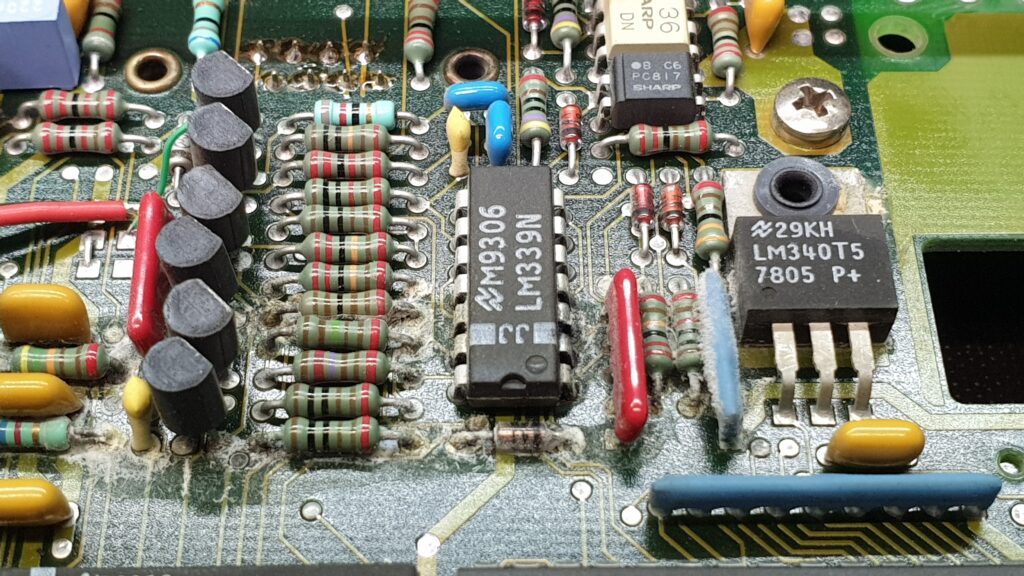
Regeneracji lub wymianie podlegać będą również elementy pasywne, takie jak drabinka rezystorów oraz niektóre kondensatory, co można ocenić na podstawie zdjęcia poniżej.
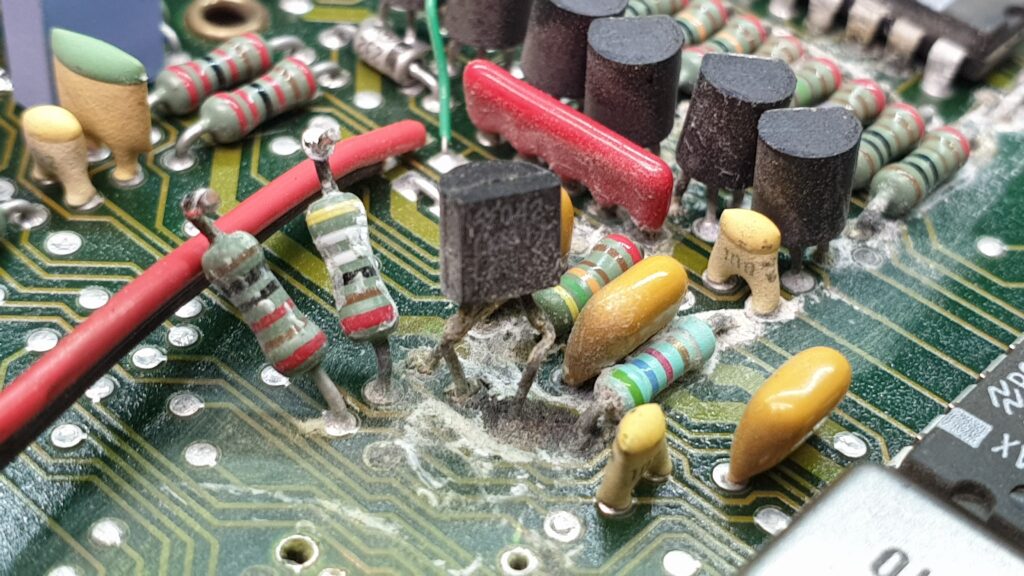
Pierwszą czynnością naprawczą było wstępne oczyszczenie mechaniczne i chemiczne, oraz umycie płyty w celu oceny przydatności elementów do ponownego montażu lub zakwalifikowania do wymiany. Następnie wykonano demontaż tych elementów. W tym momencie ocenie poddano stan ścieżek i przelotek (vias), które wcześnie nie były widoczne.
Między innymi wykonano pomiary ciągłości połączeń elektrycznych poprzez badanie rezystancji połączeń pomiędzy elementami.
Ze zdjęcia poniżej widać wiele fragmentów struktury elementów przewodzących PCB, które będą wymagały regeneracji lub wręcz odtworzeniu.
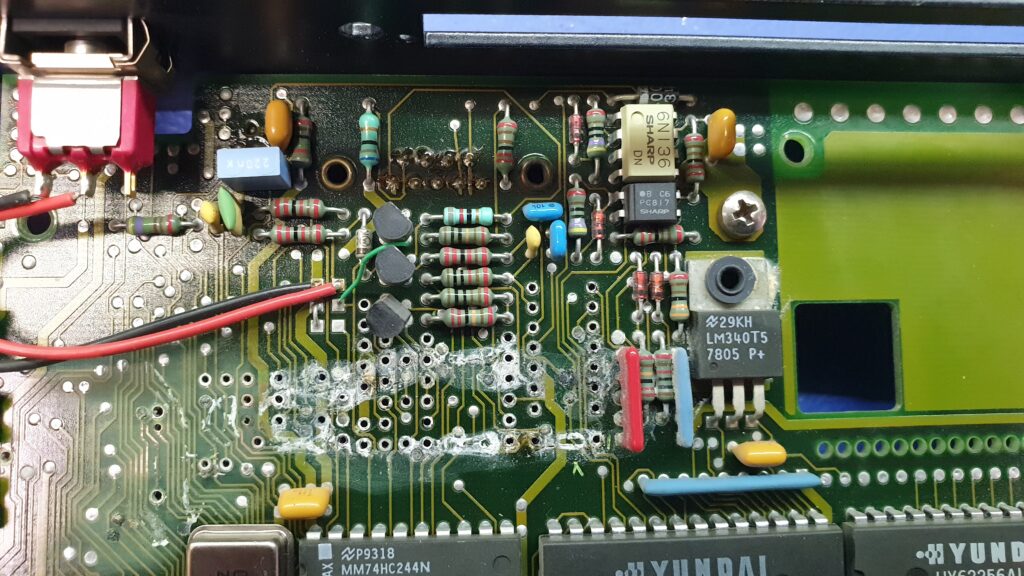
W kolejnym procesie płytka została szczegółowo umyta w myjce ultradźwiękowej, z zastosowaniem kąpieli w wysokoprocentowym stężeniu Isopropanolu, w temperaturze 50st.C. Następnie płytkę wysuszono strumieniem powietrza pod wysokim ciśnieniem, celem usunięcia frakcji stałych, które mogły jeszcze znajdować się na jej powierzchni.
Poniżej widzimy PCB od strony warstwy elementów (top / elements side), bezpośrednio po wykonaniu opisanych wcześniej czynności. Tak przygotowana płytka jest gotowa do przeprowadzenia naprawy warstwy przewodzącej, na którą składają się ścieżki wraz z przelotkami.
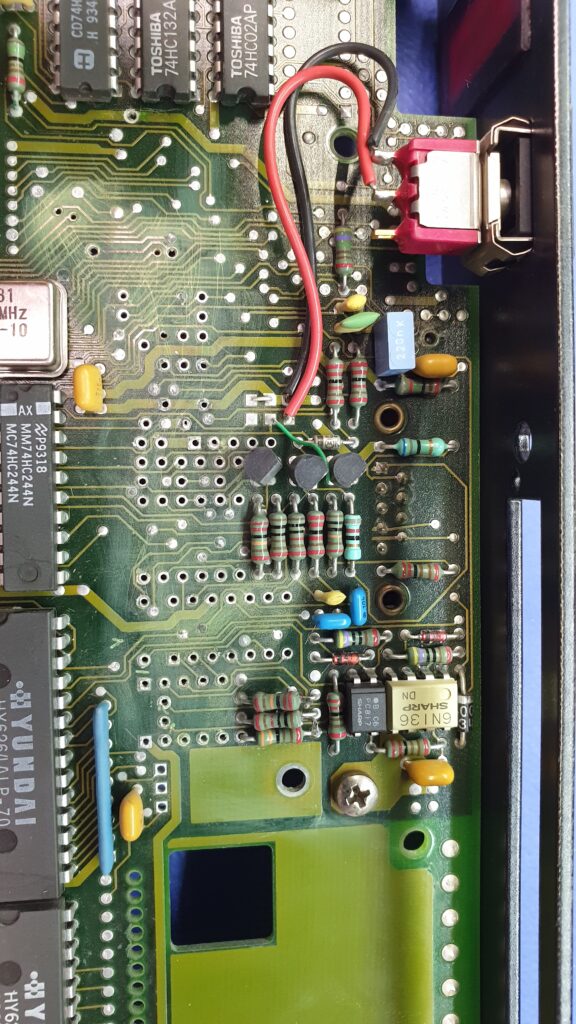
Na zdjęciach poniżej widzimy kolejne etapy naprawy uszkodzonych ścieżek i przelotek płytki PCB. Warto dodać, że analogiczne procesy naprawcze, jak te widoczne na stronie elementów (top side), dotyczą również płytki PCB od dolnej strony miedzi (bottom side).
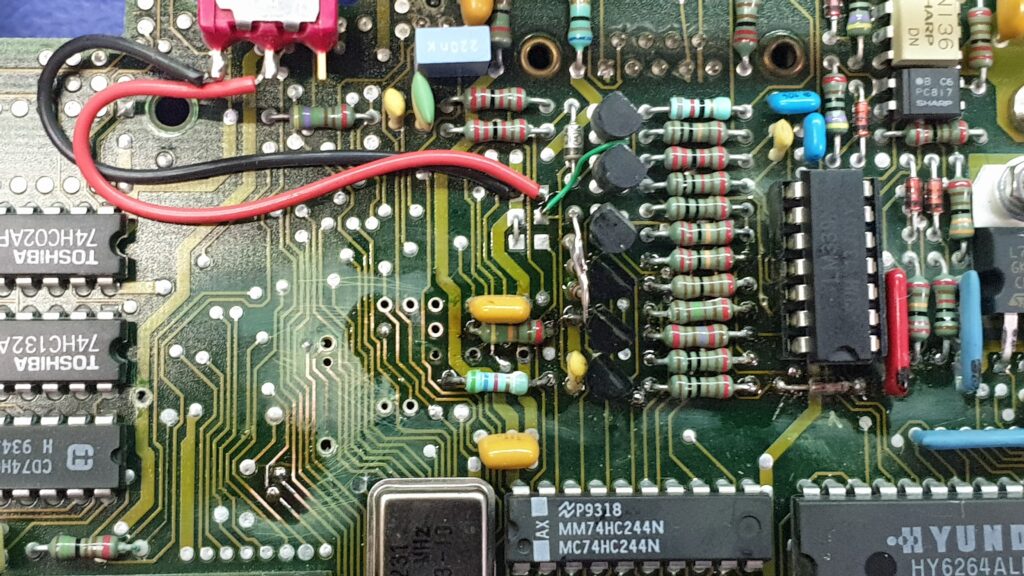
Regeneracja przelotek polega na usunięciu z ich wnętrza cyny wraz z wytworzonymi produktami korozji, następnie oczyszczeniu z pozostałości tlenków oraz lakieru solder maski każdej z nich z obydwóch stron płytki i po pokryciu fluksem, pocynowaniu tak przygotowanych miejsc. Po wykonaniu tego procesu dla wszystkich przelotek, płytka jest myta kolejny raz w celu usunięcia pozostałości chemii fluksa, co jest niezbędne przed zabezpieczeniem kocowym płyty lakierem poliuretanowym.
Zdjęcie poniżej pokazuje płytkę PCB z naprawionymi warstwami przewodzącymi oraz po zamontowaniu wymienionych, bądź zregenerowanych elementów elektronicznych, a także częściowym pokryciu warstwą antyadhezyjną (w tym przypadku jednoskładnikowym lakierem poliuretanowym, którego kolejne warstwy zostaną naniesione na płytkę metoda natryskową).
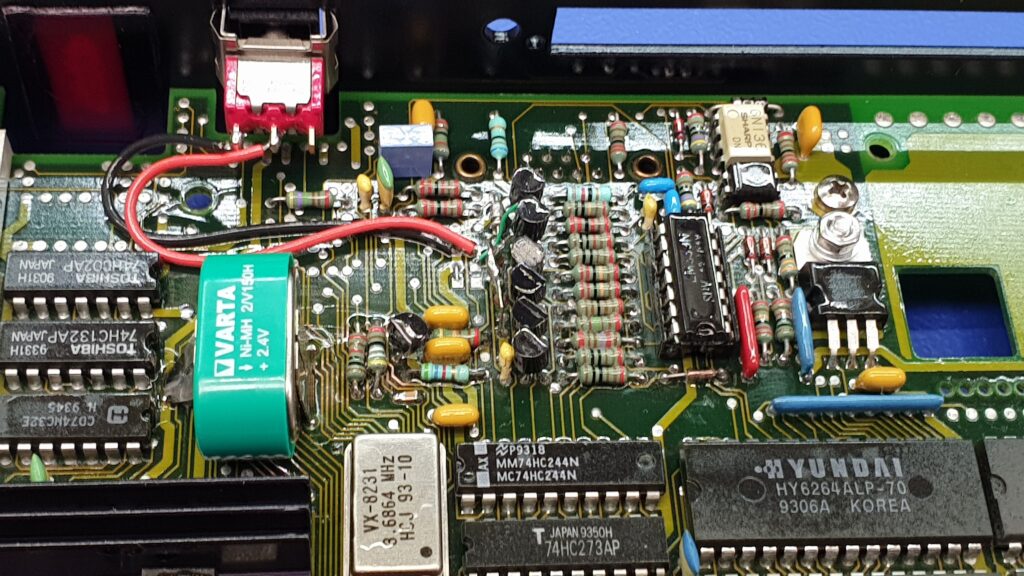
Po zabezpieczeniu płytki przed ponownym narażeniem na ewentualny kontakt z cieczą dokonaliśmy również sprawdzenia połączeń w newralgicznych miejscach płyty, wykorzystując do tego celu wykonane wcześniej uproszczone schematy połączeń, takie jak ten przykładowy, pokazany poniżej.
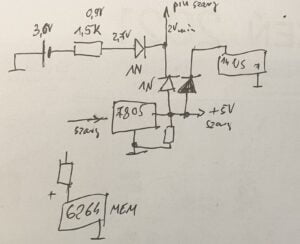