Tester inwerterów – Wersja B (v4.2)
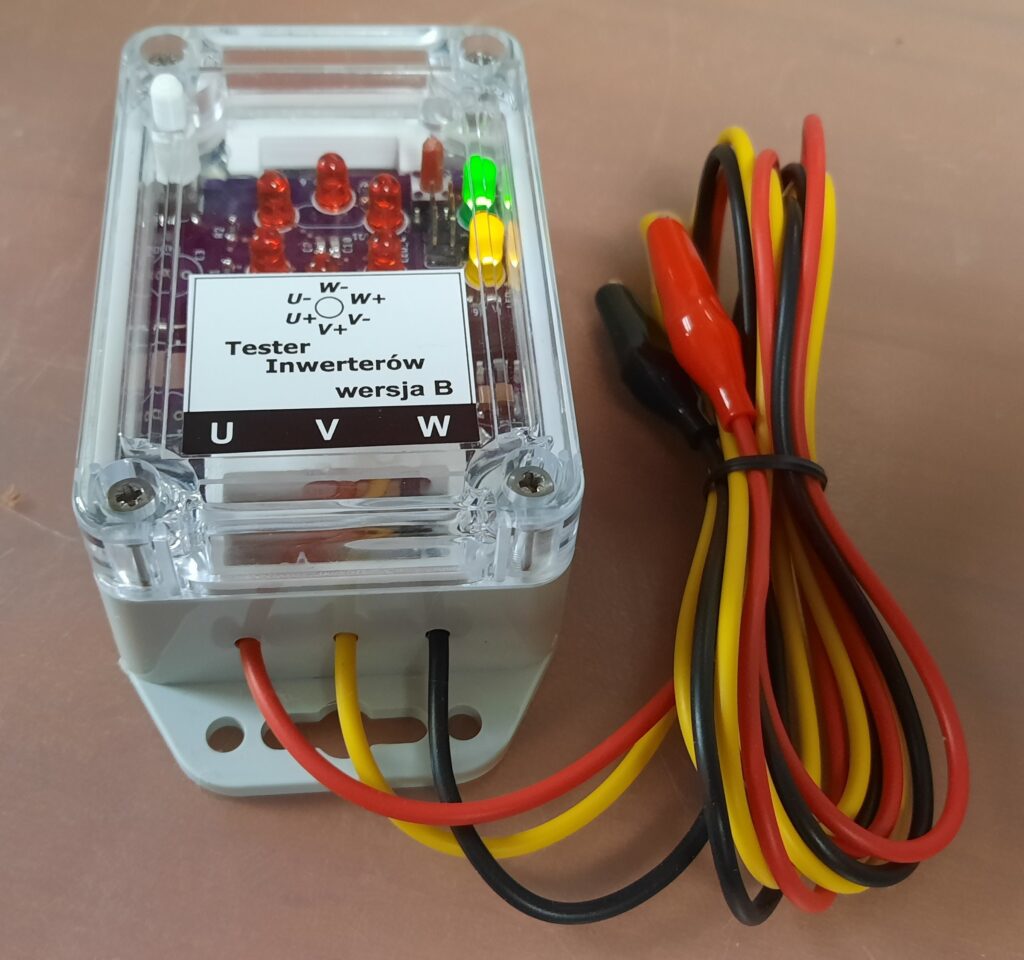
Tester Inwerterów w wersji B (wersja oprogramowania v4.2) jest zmodernizowaną, mikroprocesorową wersją poprzedniego testera w wersji A. Testery w obydwóch wersjach są uniwersalnym narzędziem, przydatnym przy sprawdzaniu działania przede wszystkim takich elementów napędów (w tym HVAC) jak: Inwertery (falowniki / sterowniki silników np. kompresorów lub wentylatorów), dotyczy to zarówno sterowników napędów trójfazowych, jak i jednofazowych, prądu przemiennego (AC) oraz zmiennego i stałego (DC).
Różnica polega na tym, że w wersji B można dodatkowo oglądać wyniki „zapamiętane” w czasie testowania, co daje możliwość testowania nawet bardzo krótkich sygnałów podawanych przez inwerter na silnik (np. w lodówkach, lub innym sprzęcie AGD oraz HVAC). Jest to ważne, gdyż większość inwerterów (np. wszystkich lodówek) w razie ewentualnej awarii podaje zasilanie na kompresor jedynie przez bardzo krótką chwilę, po czym uruchamia zabezpieczenie wyłączające to zasilanie, w celu zabezpieczenia przed zniszczeniem obwodów elektronicznych inwertera i/lub uzwojeń samego kompresora.
Ponieważ tester w wersji B jest wyposażony w mikrokontroler, wymaga on źródła zasilania prądu stałego.
Obecnie dostępna jest opcja z zasilaniem akumulatorowym (akumulator LiPo) i zintegrowanym układem ładowania poprzez złącze USB-C.
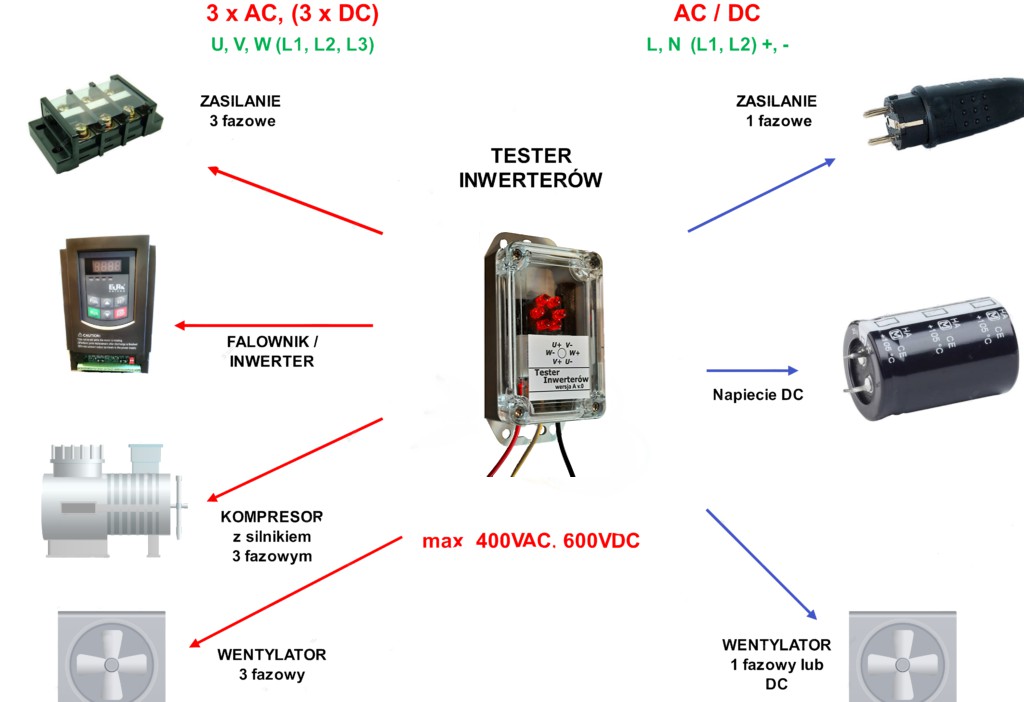
Właściwości użytkowe.
- Wykrywanie i zapamiętywanie krótkich impulsów z testowanego inwertera (w przeciwieństwie do wersji A, widoczne są impulsy przechwycone zanim jeszcze zadziała zabezpieczenie inwertera)
- Obrazowanie w czasie rzeczywistym testowanych sygnałów oraz sygnałów już zapamiętanych
- Kasowanie zapamiętanych impulsów
- Wygodne zasilanie akumulatorowe
- Usypianie i budzenie urządzenia jednym przyciskiem (ponieważ urządzenie jest zasilane akumulatorkiem LiPo, uśpienie go w czasie gdy nie jest używany wydłuża czas pracy na jednym ładowaniu ogniwa)
- Łatwe podłączanie do testowanego obwodu dzięki zaciskom krokodylkowym
- Szeroki zakres wykrywanych napięć w testowanych obwodach
- Dodatkowy przycisk resetujący procesor testera
- Tester umożliwia pracę w trudnych warunkach atmosferycznych
Konstrukcja urządzenia.
Tester w wersji B składa się z obudowy, w której umieszczonych jest 8 różnokolorowych diod LED, z czego 6 czerwonych wskazuje wynik testu (ich świecenia sygnalizuje pobudzenie testowanym napięciem), zielona zaś sygnalizuje zasilanie a żółta gotowość do pracy oraz pozytywny wynik testu. Tester wyposażony jest w 3 zakończone „krokodylkami” przewody przyłączeniowe umożliwiające podłączenie testera do sprawdzanego obwodu.
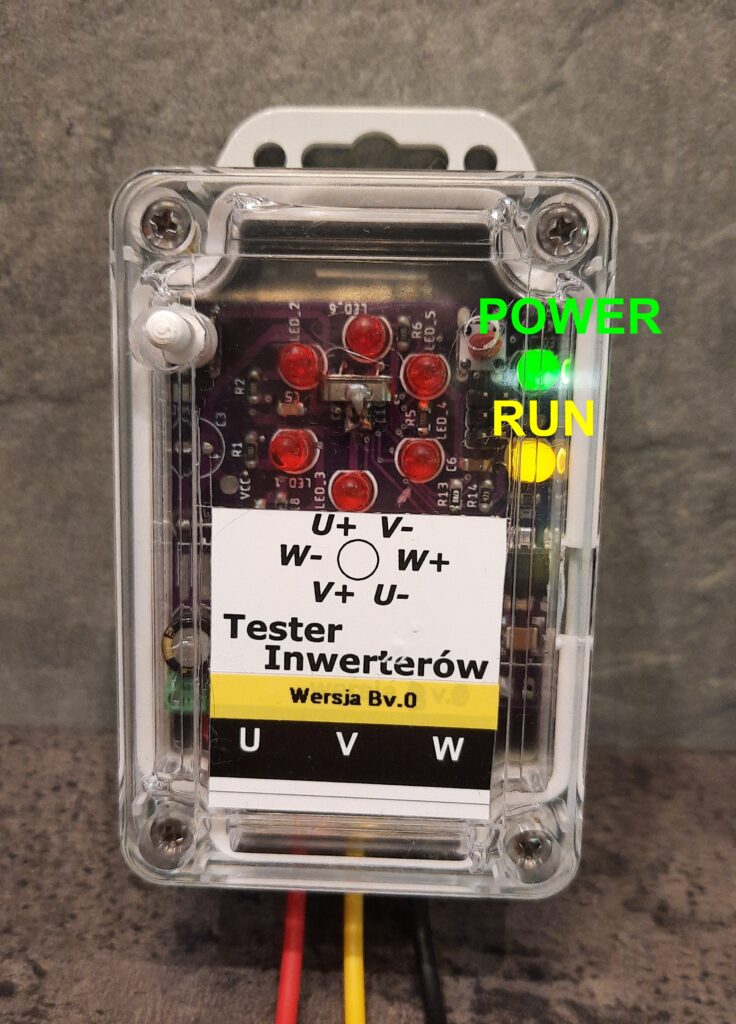
Tryby pracy testera.
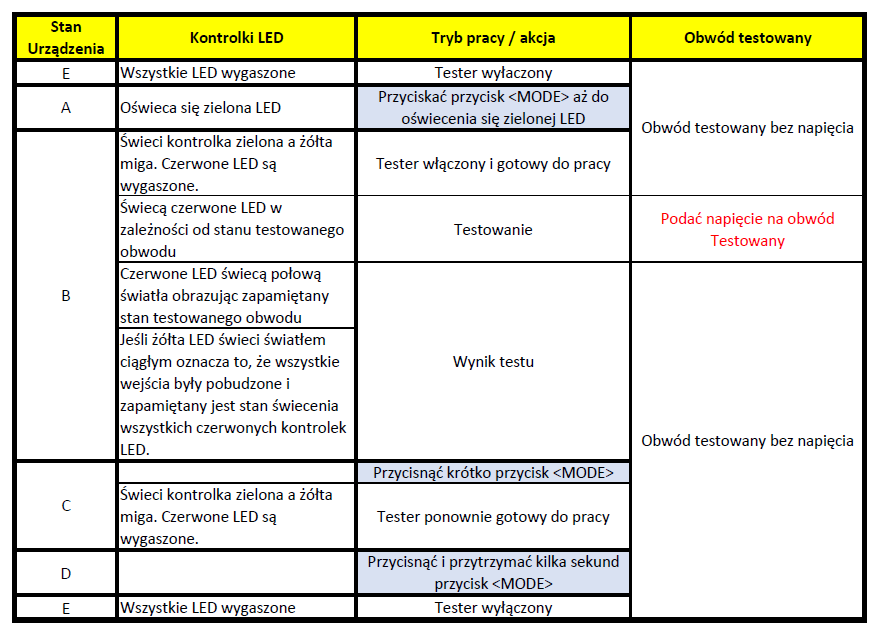
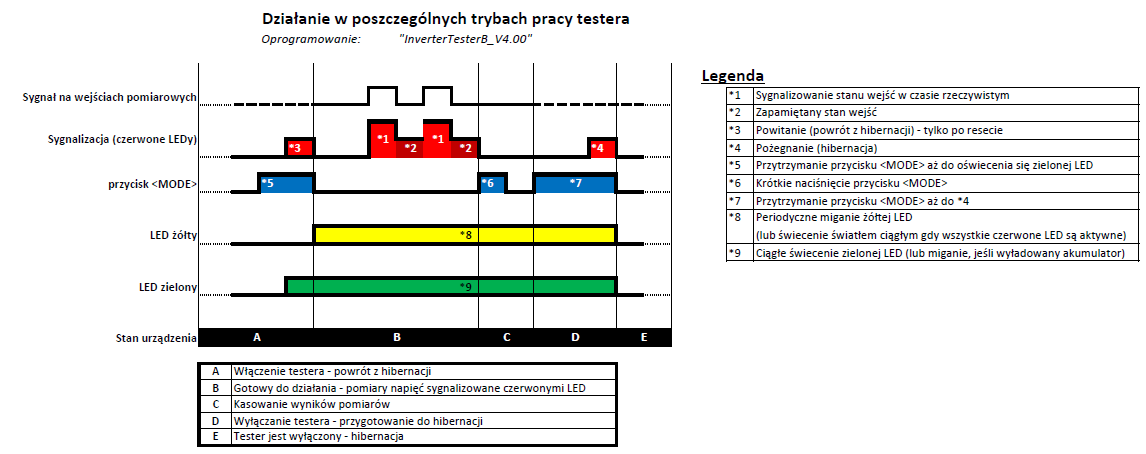
Przygotowanie do sprawdzania obwodów trójfazowych.
Tester w wersji B przyłączamy dokładnie tak samo jak w przypadku testera w wersji A, tzn. zgodnie z opisami przewodów, które przedstawia fot. niżej, tzn. przewód „U” (czerwony) łączymy z wyjściem inwertera oznaczonym jako „U” lub z zaciskiem zasilania trójfazowego AC oznaczanym zwykle jako „L1” lub „R”, zaś przewody „V” i „W” (w kolorach odpowiednio: żółty i czarny) łączymy w analogiczny sposób z odpowiednimi zaciskami tego samego obwodu. Następnie nie włączając jeszcze zasilania trójfazowego testowanego obwodu, załączamy zasilanie wybudzając tester z hibernacji (naciskamy przycisk <MODE> aż do zaświecenia się zielonej kontrolki lub wciskamy krótko przycisk <RESET>), .
Testowanie obwodów trójfazowych.
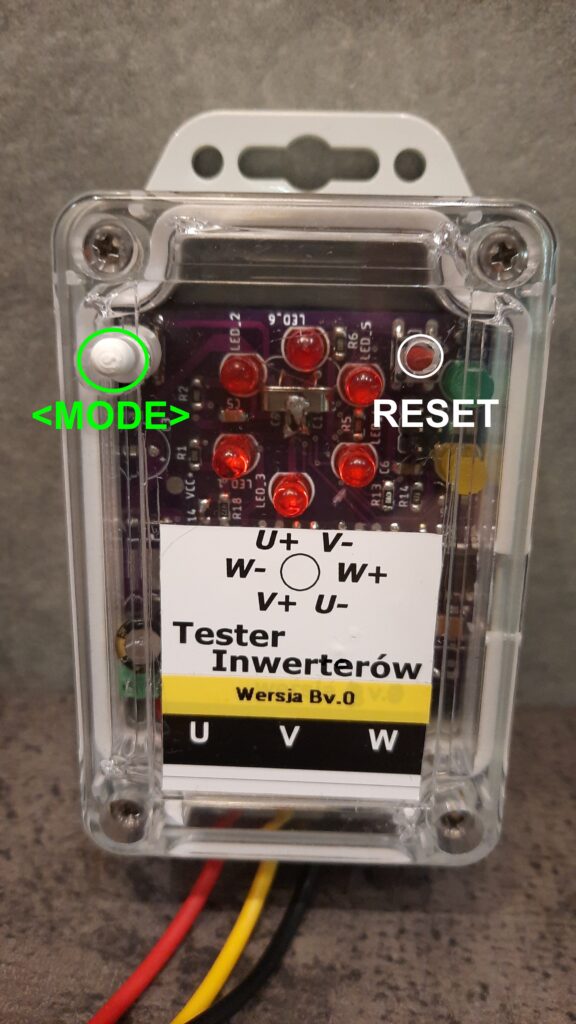
Załączanie zasilania testera odbywa się poprzez krótkie naciśnięcie przycisku <MODE> (na zdjęciu powyżej oznaczonego zielonym opisem), znajdującego się u góry, po lewej stronie obudowy.
Przycisk czerwony zaś umieszczony u góry, po prawej stronie obudowy (na zdjęciu oznaczony białym opisem) służy do resetowania testera. Jeśli zaistnieje taka potrzeba wciskamy go np. długopisem lub innym cienkim narzędziem.
Gotowość do testów sygnalizują dwie kontrolki, z których zielona powinna być oświecona (sygnalizacja zasilania), żółta zaś pulsuje sygnalizując moment wykonywania testów.
Po załączeniu testowanego napięcia U, V, W, wynik testu sygnalizowany jest oświeceniem się diod LED w kolorze czerwonym, w taki sposób, że pojawienie się napięcia na dowolnej z faz jest sygnalizowane słabym świeceniem odpowiednich LED (aż do skasowania wyników testu za pomocą krótkiego naciśnięcia przycisku <MODE>), jest to informacja o „zatrzaśnięciu” wyniku testu.
Mocne świecenie kombinacji czerwonych LED sygnalizuje bieżący wynik testu i ma charakter chwilowy.
Jeśli jednocześnie z wynikiem testu żółta dioda LED świeci światłem ciągłym, oznacza to że podczas testu na wszystkich fazach pojawiło się napięcie, co pokazuje pozytywny wynik testu.
Wyłączanie testera.
Ponieważ tester zasilany jest akumulatorowo, posiada on możliwość wyłączenia zasilania (hibernacji mikrokontrolera) tak, aby w czasie bezczynności pobierał on jak najmniej energii.
Wyłączenie testera dokonuje się poprzez przyciśnięcie i przytrzymanie kilka sekund przycisku <MODE>.
Podczas gdy tester jest dłuższy czas włączony ale nieużywany, następuje jego samoczynne wyłączenie (hibernacja).
Po wyłączeniu tester ma wygaszone wszystkie diody LED i pobiera szczątkowy prąd z baterii (akumulatora).
Ładowanie akumulatora.
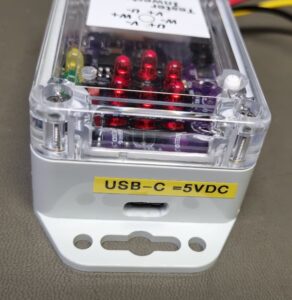
- Na tylnej ściance obudowy znajduje się gniazdo USB-C. Przy pomocy standardowego kabla z wtykami USB-A i USB-C (np. kabel do ładowania telefonów komórkowych) należy doprowadzić zasilanie +5VDC służące do kontrolowanego ładowania akumulatora Li-Po znajdującego się wewnątrz testera.
- Ładowanie sygnalizuje kontrolka czerwona widoczna w okolicy złącza USB-C. Kolor niebieski zaś, informuje o zakończeniu ładowania akumulatora, należy odłączyć kabel ładowania.
- Jeśli w czasie ładowania wydziela się zbyt duża ilość ciepła z urządzenia lub daje się odczuć nieprzyjemny zapach lub inne anomalia, należy natychmiast odłączyć zasilanie ładowania poprzez wyjęcie wtyczki z gniazda USB-C. W takim wypadku nie wolno użytkować testera aż do zdiagnozowania uszkodzenia i wykonania naprawy w autoryzowanym serwisie producenta.
- Jeśli tester wyłączy się w czasie normalnej pracy lub zielona kontrolka LED przestanie świecić, należy naładować akumulator.
Testowanie obwodów jednofazowych.
W tym przypadku przewód testera oznaczony jako „U” (w kolorze czerwonym) podłączamy do zacisku zasilania AC oznaczonym w badanym urządzeniu jako „L” lub zacisku napięcia stałego DC oznaczonym jako „+” lub „DC+” lub „P+”. Natomiast żółty przewód testera oznaczony jako „V” podłączamy do zacisków oznaczonych jako „N” w obwodach AC lub „-” albo „DC-” albo „N” w obwodach prądu stałego DC.
Zacisk testera oznaczony jako „W” (czarny) musi zawsze pozostawać niepodłączony.
Uwaga !
Przewód testera w kolorze czarnym, oznaczony jako „W” we wszystkich pomiarach jednofazowych nie może być podłączany do żadnego obwodu. Proszę upewnić się, że przewodząca prąd końcówka krokodylkowa jest dobrze zaizolowana i nie zwiera się np. z żadną częścią metalową, mogącą przewodzić prąd elektryczny.
Wyniki sprawdzania obwodów Testerem Inwerterów.
Poprawny wynik podczas sprawdzania obwodów testerem pokazano w tabeli poniżej.
Rodzaj testowanego obwodu | Podłączone zaciski | Poprawne wskazania testera |
---|---|---|
Trójfazowy AC | U, V, W | Wszystkie LED świecą |
Jednofazowy AC | U, V | 4 LED świecą (U+,U-,V+,V-) |
Jednofazowy DC | U, V | 2 LED świecą * (U+,V- lub U-, V+) |
Aby uzyskać poprawne wyniki pomiaru, w sprawdzanym obwodzie musi występować napięcie większe od 100VDC i nie może ono przekraczać 400VAC (600VDC). Świecenie diod LED podczas testowania obwodów trójfazowych jest równoznaczne z przepływem prądu w danej gałęzi, tak jakby odbiorniki były połączone w „gwiazdę” (patrz rys. poniżej).
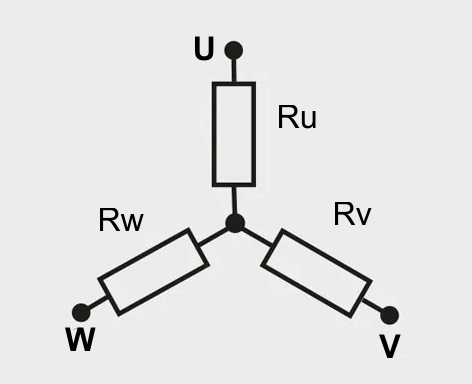
Możliwe jest przyłączanie testera równolegle z silnikiem lub innym odbiornikiem prądu w celu bieżącego monitorowania zasilania tego odbiornika.
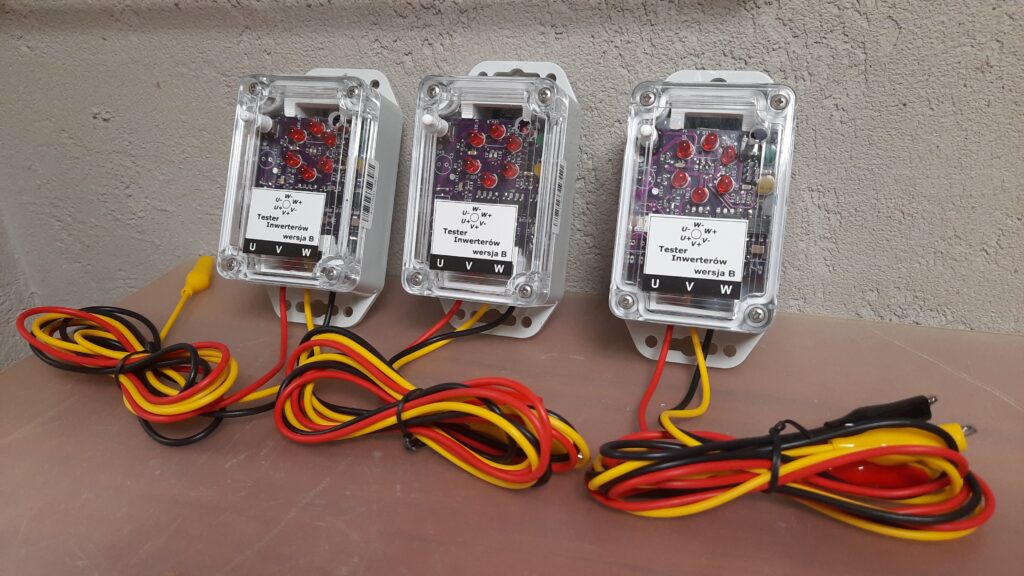
Uwaga !
Zachowaj ostrożność – pracujesz z napięciami niebezpiecznymi dla życia. Przed przyłączaniem testera upewnij się, że w testowanym obwodzie nie występuje napięcie (do tego celu służą certyfikowane przyrządy pomiarowe). Na czas pracy zabezpiecz siebie i otoczenie przed działaniem wysokiego napięcia, zwłaszcza kiedy pracujesz w trudnych warunkach, np. na wysokości, na mokrej powierzchni. Używaj środków ochrony osobistej i dbaj o stosowanie zasad BHP, które m.in. dotyczą pracy z niebezpiecznym dla życia napięciem.
Pamiętaj !
Wszystko co robisz, robisz na własną ODPOWIEDZIALNOŚĆ. Twoje decyzje mogą mieć nieodwracalny skutek – zachowaj maksymalną ostrożność !
Przykład testowania obwodów AC i DC jednostki zewnętrznej klimatyzatora.
Poprawny wynik wszystkich testów w obwodach oznaczonych strzałkami sugeruje poprawne działanie sterowania silnikiem sprężarki. Jeśli nadal występują nieprawidłowości w pracy sprężarki, najprawdopodobniej jest ona uszkodzona.
Analogiczny układ jak poniższy, może występować także w przypadku sterowania wentylatorem / wentylatorami.

Aby uzupełnić wiedzę na prezentowany temat zachęcamy do przeczytania artykułu „Diagnoza napędów z falownikami„.